Your Temperature Measurement Experts
Mini Case Studies from the Field
Non-intrusive Temperature Measurement for Cheese Manufacturing
Application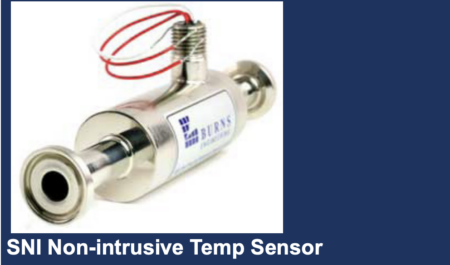
A cheese manufacturing facility use temperature sensors to control their manufacturing process throughout their plant. Direct immersion sanitary temperature sensors are mounted in tees at various points in the process lines. Near the end of the manufacturing process, the cheese becomes dense and forced through the lines at higher pressures. It is at this point where an increased force is now applied to the temperature sensor probe in the line and causes them to bend or break.
Challenge
To strengthen a direct immersion temperature sensor would require increasing the wall thickness and/or diameter of the sheath. Increasing the wall thickness would reduce the time response performance. Increasing the sheath diameter would reduce the product flow going past the probe. Mounting a surface sensor on the outside of the line requires adequate insulation from the surrounding ambient air. But since this is a sanitary environment, insulation is not an option for it becomes a potential location for bacteria to grow.
Solution
The Sanitary Non-intrusive Temperature Sensor is a surface sensor mounted on the outside of the process tube and surrounded by a protective concentric tube which thermal isolates the sensing element from the surrounding ambient air.
The SNI is mounted in line with the process and the process fluid flows freely through the tube. Since there is no probe in the process line, there is nothing to fail. The concentric housing creates a clean and sanitary thermal barrier. Time response performance can be similar to a direct immersion probe.